Pretreatment System
EQS provides a beverage pre-processing system suitable for the production of various beverages
The pretreatment system is specially designed to produce juice, tea drinks, lactic drinks, aerated drinks, etc, which includes types of equipment, such as hot-water system, sugar melting system, recovery system, extraction system, milk power reconstitution system, monosaccharide system, saccharide system, mixing and allocating system, CIP system, plate or tube UHT sterilizers, mixers, vacuum degassing and aroma recycling system, homogenizing system, and control system.
As a long-standing supplier of various single-machines and complete-line equipment for beverage treatment to beverage companies at home and abroad, EQS can offer engineering consulting and technological design services tailored to the needs of clients, such as planning of equipment configuration, layout, process and auxiliary equipment for manufacturing shops.
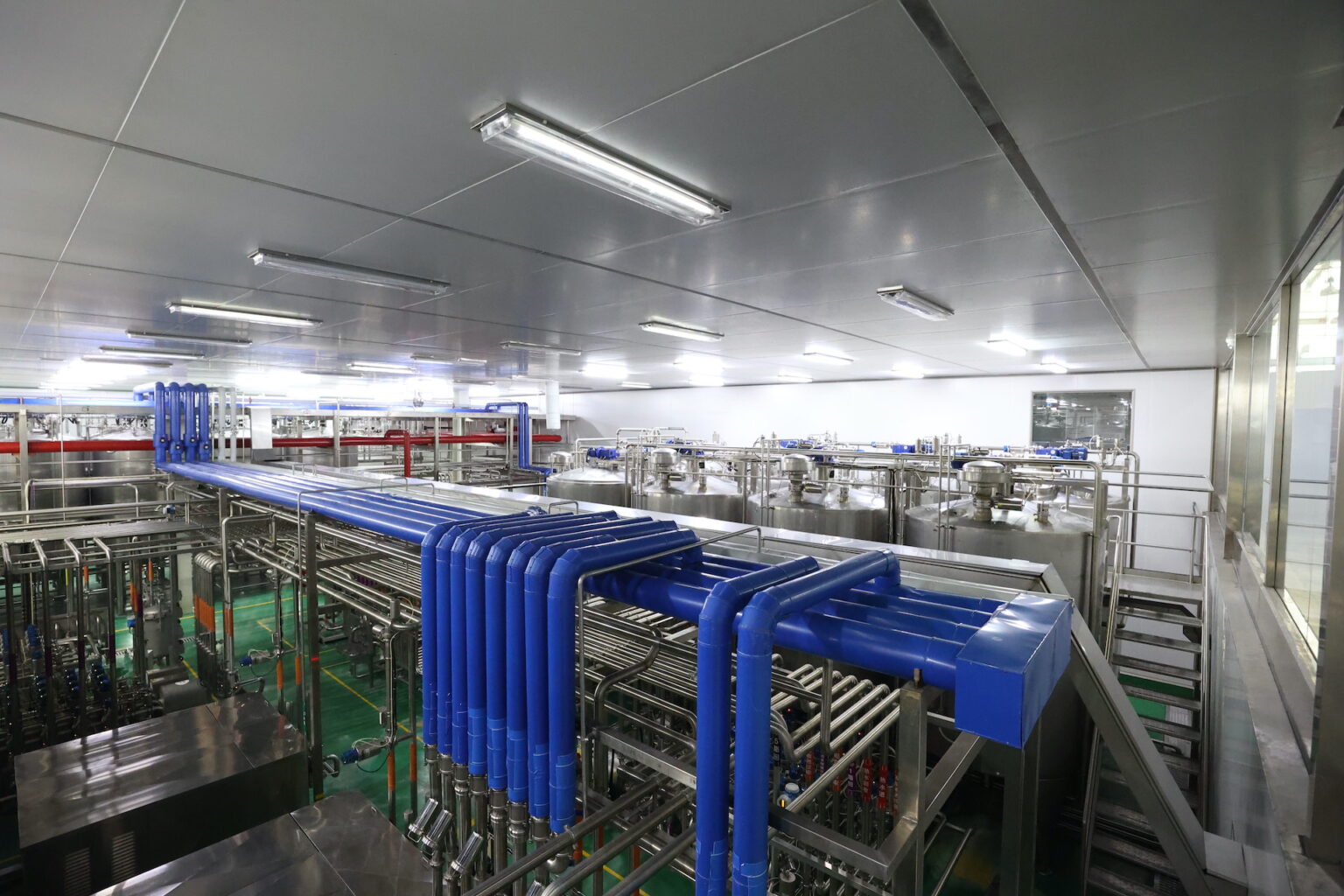
Don't hesitate to contact us for more information.
jiangsu,suzhou zhangjiagang hexi rouad - china
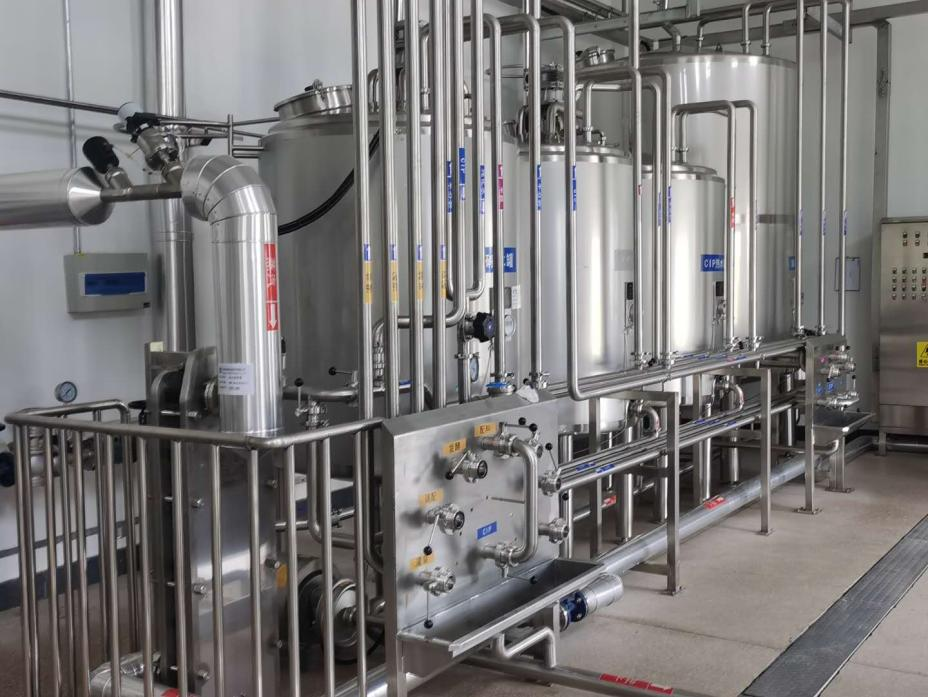
CIP cleaning is CLEAN IN PLAY (in-situ cleaning). A cleaning station is a compact modular cleaning system used for the cleaning cycle of beverage production lines, capable of performing hot and cold cleaning cycles.
This CIP cleaning workstation is automatically controlled. All cleaning process parameters (cleaning time, acid and alkali concentration, cleaning solution temperature, cleaning method) can be set on the human-machine interface. When cleaning is required, specify the required cleaning equipment on the human-machine interface, select the cleaning method, start the system, and the CIP equipment will automatically complete the cleaning process according to the pre-set program, and can automatically recover acid, alkali, and clean water in sections.
This system has automatic water replenishment and acid-base replenishment, automatic temperature adjustment, display of temperature, concentration, liquid level, simulation process status, and sound and light alarm functions. Various parameters can be modified on the human-machine interface. The manual function and parameter modification function are password protected at different levels.
Equipment Features
- Temperature Self-Control: Regulates the opening size of the steam flow control valve through outlet temperature probe detection, ensuring cleaning temperature remains within the allowable range (control accuracy ± 2 ℃).
- Real-Time Monitoring: Equipped with conductivity detectors, temperature sensors, and flow switches on the reflux pipe to provide real-time detection of key parameter values during cleaning.
- Programmed Operation: All cleaning process parameters can be set via the human-machine interface. The system automatically cleans according to the programmed settings. Multiple cleaning programs are pre-installed and can be freely combined based on actual operational needs.
- Multi-Path Connection: The CIP outlet is fitted with a porous conversion plate, enabling connection to multiple cleaning pipelines. Internal tanks are also equipped with porous conversion plates, facilitating connections to each tank’s cleaning pipelines.
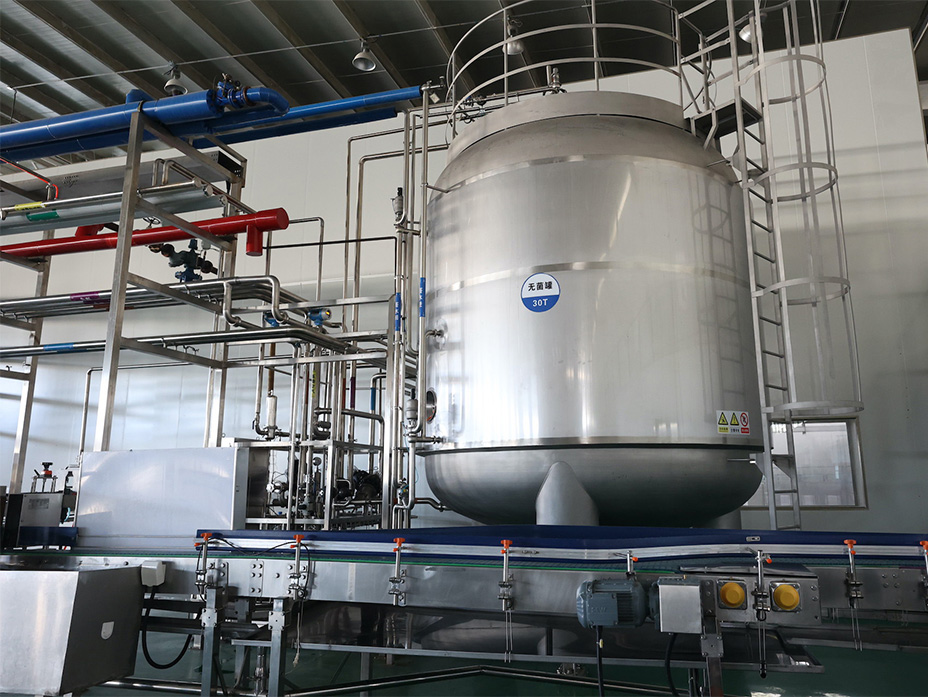
The sugar conversion system of the beverage filling production line first sends solid sugar (such as white sugar or fruit glucose syrup) into the sugar conversion tank through a sugar storage bin or vacuum conveying device, and adds hot water with mechanical stirring to quickly dissolve and form a uniform sugar solution.
The dissolved sugar solution is transferred to a mixing tank and then subjected to pasteurization or UHT instantaneous sterilization through a plate heat exchanger, killing microorganisms while retaining the flavor of the syrup
The finished syrup is temporarily stored in sterile storage tanks and transported to the mixing section of the filling line through closed pipelines. The system adopts PLC automation control and CIP cleaning system to achieve parameter adjustment (temperature, mixing speed) and regular pipeline cleaning, ensuring production continuity and food safety, while meeting industrial requirements for high energy consumption ratio and low residue.
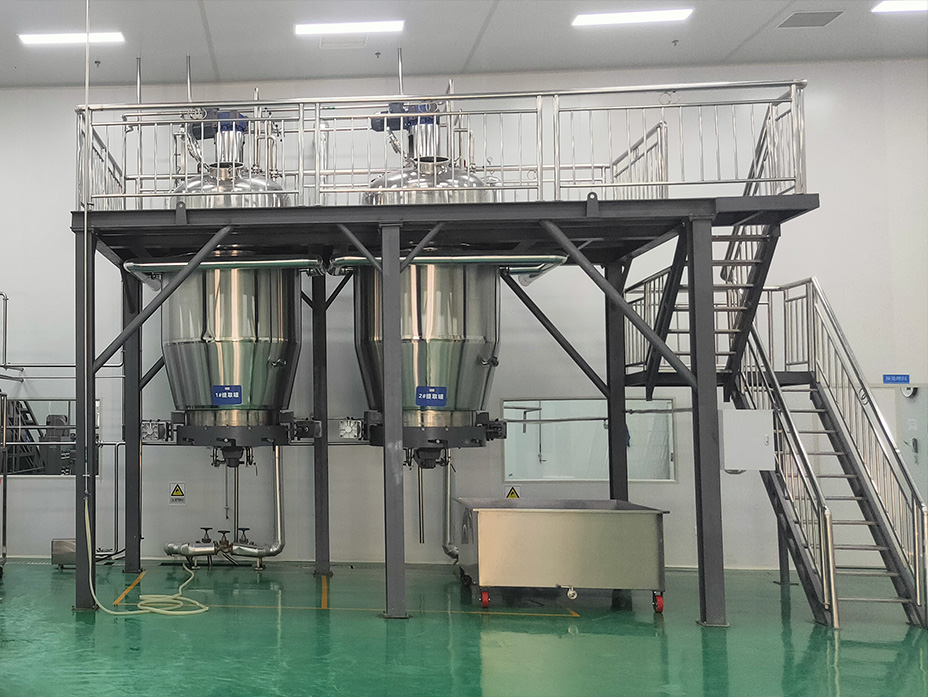
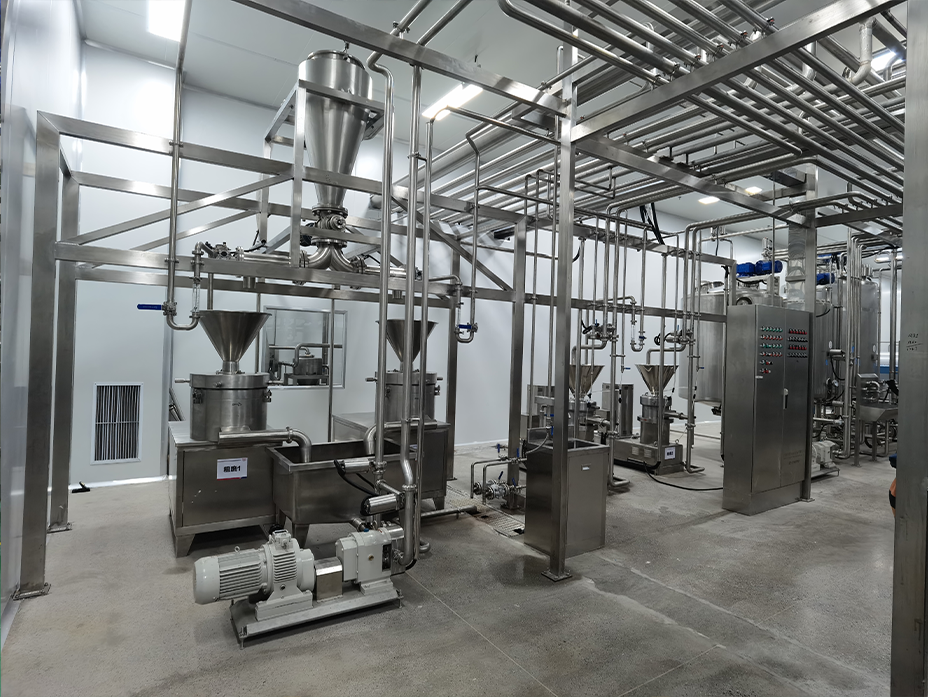
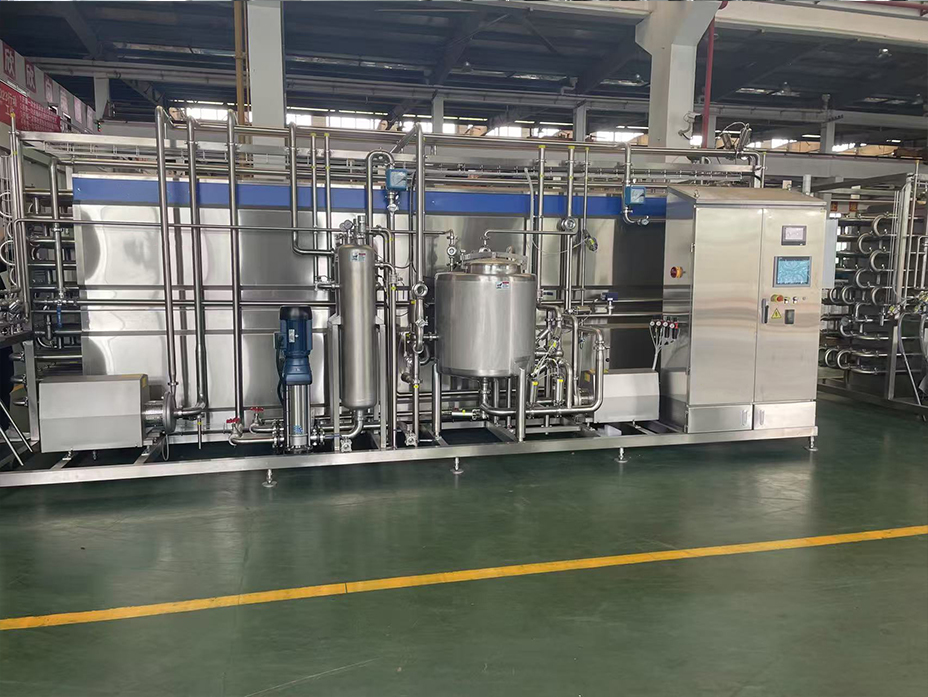
Sterilization machine is a key equipment in beverage filling production line, used to kill microorganisms (bacteria, yeast, mold, etc.), ensure product safety and extend shelf life
Equipment Features
- Fully automatic control system: The UHT ultra-high temperature tube sterilizer adopts a true human-machine dialogue system, which is easy to operate. Any operator only needs simple training to be on duty..
- High degree of automation: The equipment is equipped with a fully automatic alarm and fault handling system, which can effectively prevent the output of unqualified products and ensure the reliability of product quality.
- Cleaning function: Equipped with a CIP system, it can achieve automatic in-situ cleaning at any time without relying on the CIP system of the workshop main circuit to start.
- Communication interface: It is equipped with a communication interface with the aseptic packaging machine to achieve communication linkage with the aseptic packaging machine and ensure the reliability of product output.
- Easy maintenance: The maintenance process is simple and convenient, only the O-ring needs to be replaced, without any bulky tools.
- Efficient Heat Transfer: A tubular heat exchanger that operates in turbulent flow with materials and heat transfer media, resulting in high heat transfer efficiency, reduced scaling, and extended continuous operation time of the sterilizer.
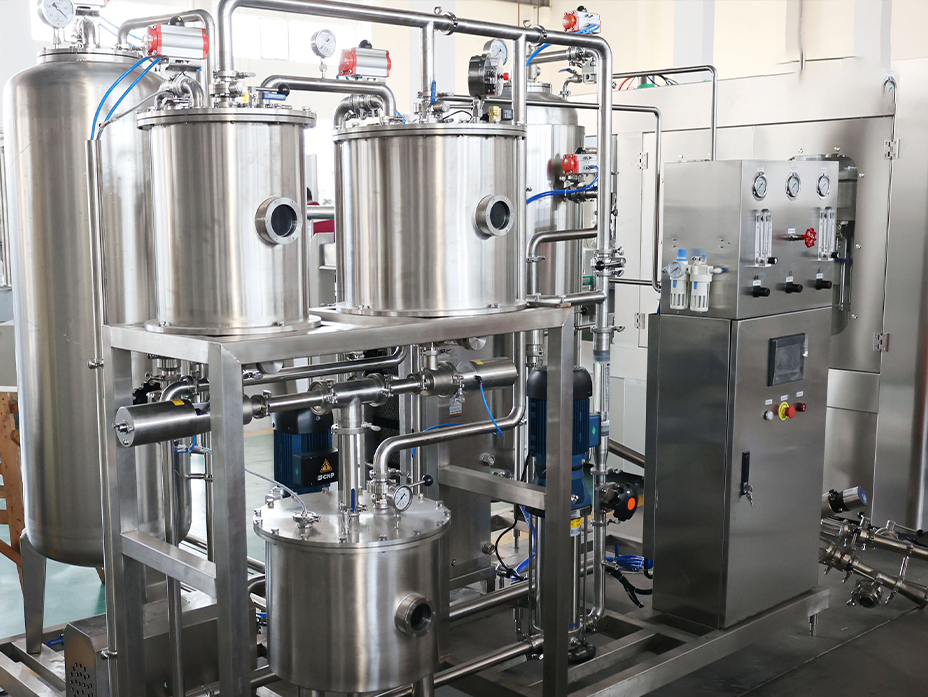
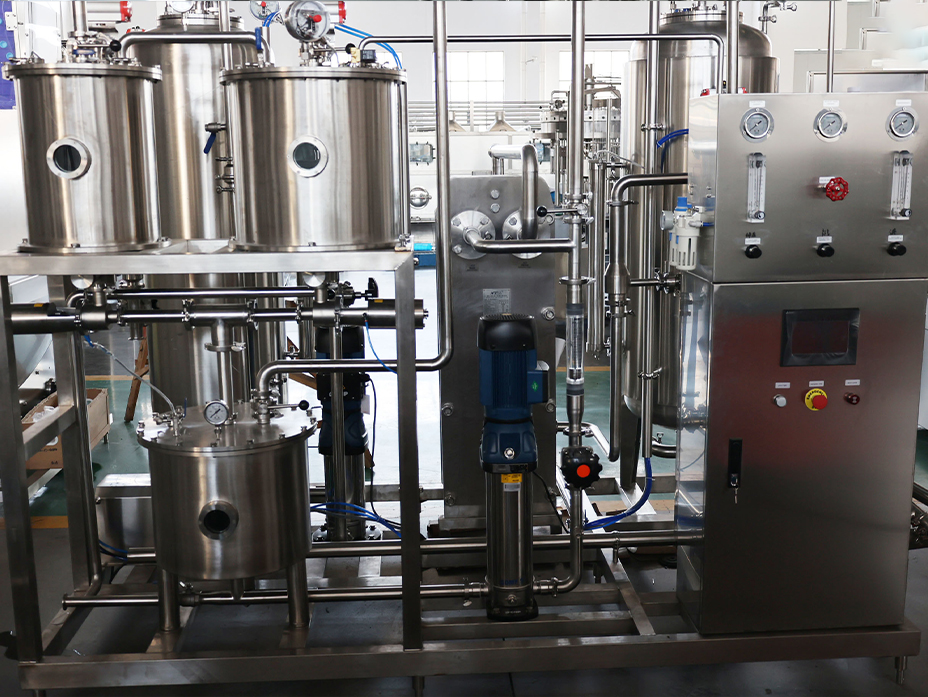
Machine Advantages
- High Efficiency: High deoxidation efficiency and good carbonization effect.
- Automated Control: The tank is equipped with automatic regulating devices for liquid level and pressure. PLC monitors the mixing process throughout.
- Precise Mixing: Uniform mixing and high proportioning accuracy.
- Eco-Friendly Carbonization: Carbonization in the pipeline is adopted to reduce CO2 emission, conducive to energy saving.
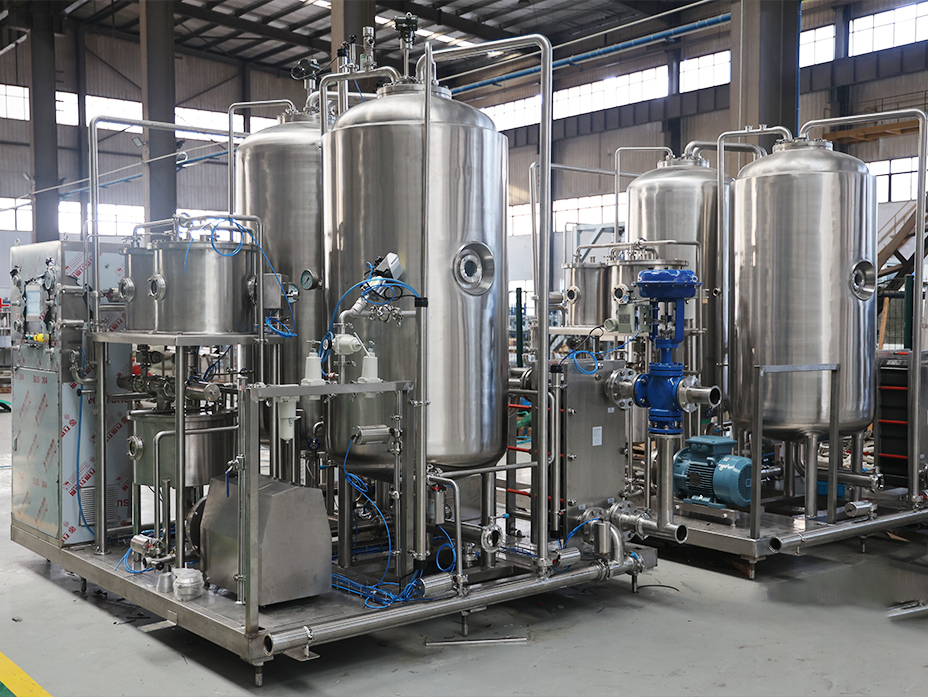
Technical Features
- Advanced Static Mixer: Utilizes advanced chemical industry static mixer (carbonizer) technology, featuring large gas-liquid mass transfer area, low resistance loss, high efficiency, low energy consumption, and simple structure. Equipped with a reliable, low-noise multistage centrifugal pump for optimal performance.
- Precise Proportioning: Features high-precision proportional needle valves and pneumatic angle valves in the syrup and water pipelines for accurate mixing ratio adjustment and prevention of cross-flow, ensuring sensitive and reliable operation.
- Atomization Deoxidation: Employs atomization deoxidation, conserving carbon dioxide gas and effectively deoxidizing water for improved pre-carbonization results.
- Adjustable Air Content: Allows easy adjustment of beverage air content through appropriate operation, catering to specific beverage requirements.
- Automated Control System: Equipped with a comprehensive automatic control system for coordinated action, simple structure, continuous production, and high automation.