Exploring the Various Types of Filling Machines Used in Beverage Production
leading paragraph:
So many drinks, so many machines! Let's explore the world of beverage filling tech.
snippet paragraph:
Filling machines in beverage production are diverse and tailored to specific needs. Common types include water filling machines, juice hot filling machines, carbonated filling machines
, beer filling machines, oil filling machines, wine filling machine, blow-fill-seal combiblock machines, aseptic filling machines, and ultra-clean filling machines.
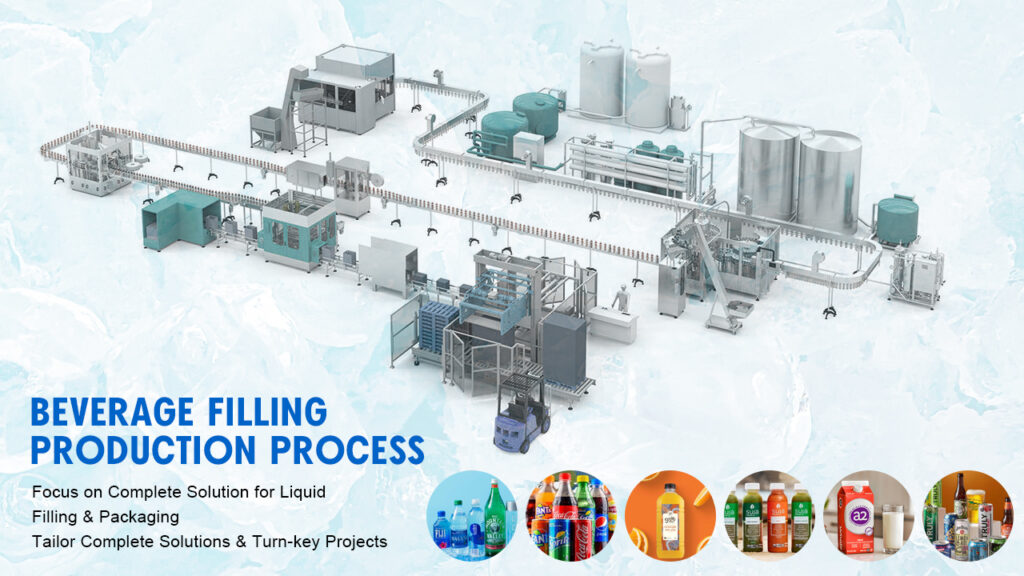
Transition Paragraph:
Each type of filling machine plays a crucial role in ensuring the quality and safety of the final product. Let's take a closer look.
Water Filling Machines: The Foundation of Hydration
leading paragraph:
Pure and simple! How do you fill water bottles efficiently?
snippet paragraph:
Water filling machines are designed for high-speed and hygienic filling of water bottles. They often include features like UV sterilization and multi-stage filtration to ensure water purity and prevent contamination.
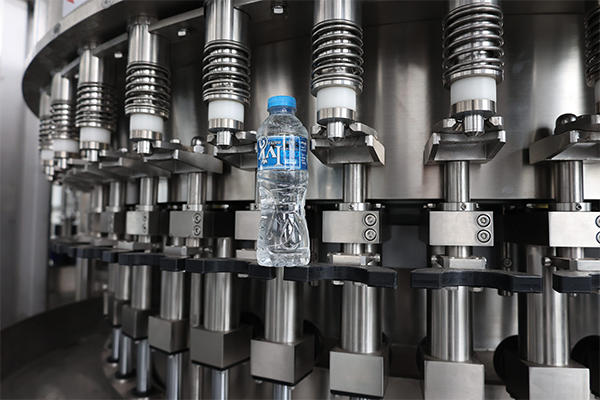
Key Features
- High-Speed Filling: Efficient production.
- UV Sterilization: Ensuring purity.
- Multi-Stage Filtration: Removing impurities.
- Hygienic Design: Preventing contamination.
- Automated Controls: Precise operation.
- Versatile Bottle Sizes: Adapting to needs.
Dive deeper Paragraph:
Water filling machines form the backbone of the bottled water industry, designed for high-speed and hygienic filling of water bottles. These machines incorporate several key features to ensure the purity and safety of the water. UV sterilization is a common component, using ultraviolet light to kill bacteria and microorganisms that may be present in the water. Multi-stage filtration systems further enhance water purity by removing impurities, sediments, and other contaminants. The machines are designed with smooth surfaces and minimal crevices to prevent the buildup of bacteria, and they often include automated cleaning cycles to maintain a sterile environment.
Juice Hot Filling Machines: Preserving Flavor and Freshness
leading paragraph:
Hot off the press! How to keep juice fresh during filling?
snippet paragraph:
Juice hot filling machines fill containers with juice at high temperatures (around 85-95°C) to sterilize the juice and container, extending shelf life without preservatives. This process requires precise temperature control and specialized equipment.
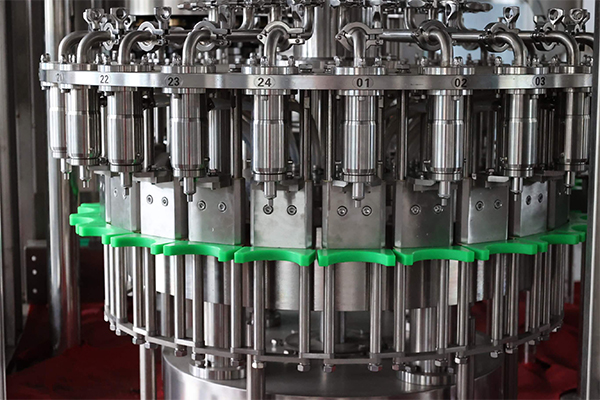
Hot Filling Essentials
- High-Temperature Filling: Sterilization.
- Precise Control: Maintaining temperature.
- Extended Shelf Life: No preservatives needed.
- Specialized Equipment: Heat-resistant materials.
- Automated Systems: Consistent performance.
- Quality Assurance: Safe and flavorful juice.
Dive deeper Paragraph:
Juice hot filling machines are specifically designed to fill containers with juice at elevated temperatures, typically ranging from 85 to 95 degrees Celsius. This high-temperature filling process serves to sterilize both the juice and the container, effectively eliminating any microorganisms that could cause spoilage. By sterilizing the product and the packaging, hot filling significantly extends the shelf life of the juice without the need for chemical preservatives.
Carbonated Filling Machines: Capturing the Fizz
leading paragraph:
Bubbly perfection! How do you keep the fizz in carbonated drinks?
snippet paragraph:
Carbonated filling machines are designed to handle the unique challenges of filling carbonated beverages. They maintain high pressure to prevent CO2 from escaping, minimizing foaming and ensuring consistent carbonation levels in the final product.
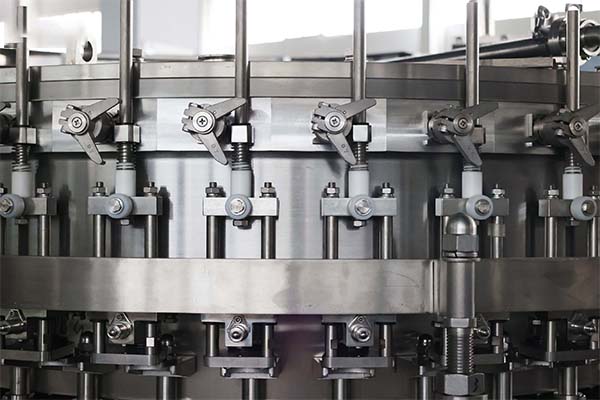
Key Considerations
- High-Pressure Filling: Preventing CO2 loss.
- Foam Reduction: Minimizing bubbles.
- Consistent Carbonation: Maintaining levels.
- Specialized Nozzles: Controlled dispensing.
- Automated Systems: Precise adjustments.
- Quality Control: Ensuring fizz.
Dive deeper Paragraph:
Carbonated filling machines are engineered to address the specific challenges associated with filling carbonated beverages. The primary goal is to maintain the carbon dioxide (CO2) dissolved in the beverage throughout the filling process. These machines operate under high pressure to prevent the CO2 from escaping, which would lead to foaming and a loss of carbonation.
beer filling machine: Protecting the Brew
leading paragraph:
Cheers to beer! How do you fill beer bottles without losing quality?
snippet paragraph:
Beer filling machines are designed to minimize oxygen exposure, which can degrade the beer's flavor and aroma. They often use counter-pressure filling and pre-evacuation techniques to maintain beer quality and prevent oxidation.
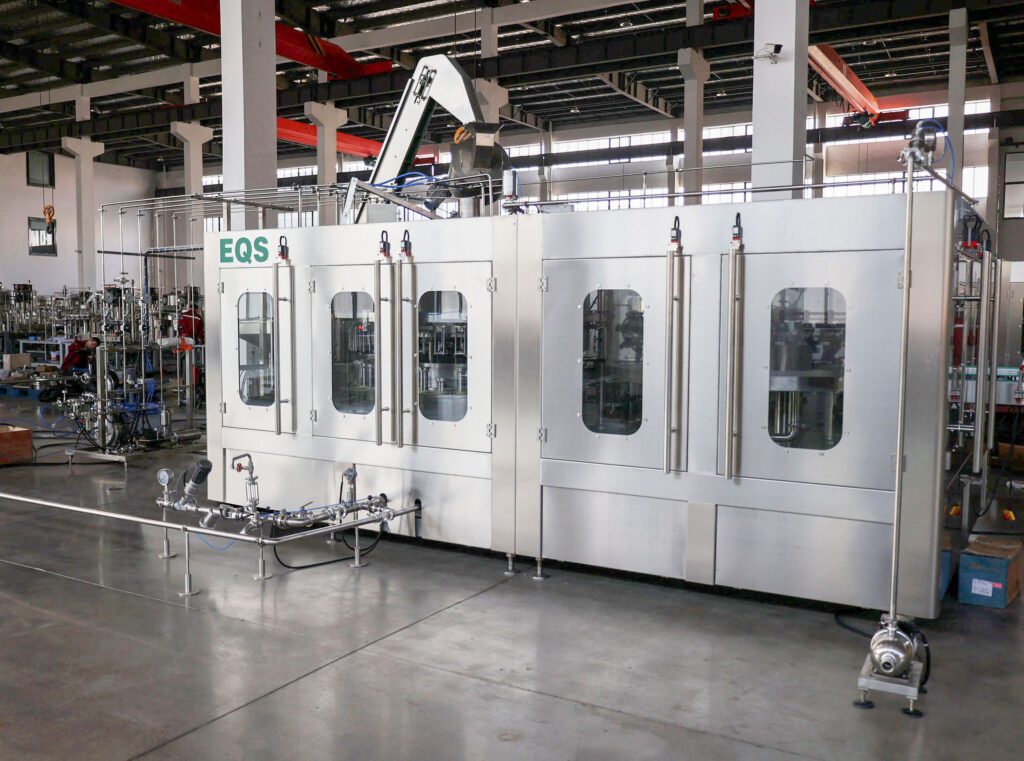
Essential Features
- Counter-Pressure Filling: Reducing oxygen.
- Pre-Evacuation: Removing air.
- Flavor Preservation: Maintaining quality.
- Specialized Nozzles: Gentle dispensing.
- Automated Systems: Consistent performance.
- Quality Control: Ensuring great taste.
Dive deeper Paragraph:
Beer filling machines are designed with a primary focus on minimizing oxygen exposure, which can significantly degrade the beer's flavor and aroma over time. Oxidation is a major concern in beer production, as it leads to the formation of off-flavors and aromas, such as cardboard or stale notes, which can ruin the drinking experience. To combat this, beer filling machines employ several techniques to reduce oxygen pickup during the filling process.
Oil Filling Machines: Precision and Cleanliness
leading paragraph:
Smooth and precise! How do you accurately fill oil containers?
snippet paragraph:
Oil filling machines are designed for accurate and clean filling of various types of oils. They often use positive displacement pumps and no-drip nozzles to prevent spills and ensure precise fill volumes.
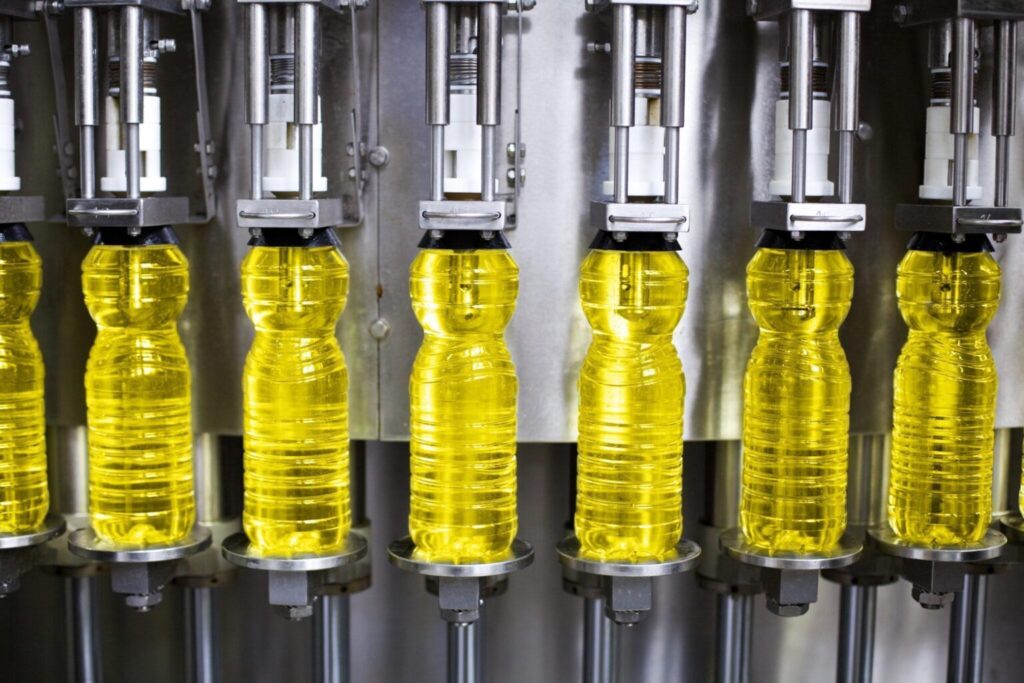
Key Attributes
- Positive Displacement Pumps: Accurate filling.
- No-Drip Nozzles: Preventing spills.
- Clean Filling: Maintaining hygiene.
- Versatile Oils: Handling different viscosities.
- Automated Systems: Consistent performance.
- Quality Control: Ensuring precision.
Dive deeper Paragraph:
Oil filling machines are specifically designed for the accurate and clean filling of various types of oils, ranging from vegetable oils to lubricating oils. These machines prioritize precision and cleanliness to prevent spills, minimize waste, and ensure that the oil maintains its quality throughout the filling process. Positive displacement pumps are commonly used in oil filling machines due to their ability to deliver highly accurate fill volumes, regardless of changes in viscosity or temperature.
Wine Filling Machines: Elegance and Preservation
leading paragraph:
To the last drop! How do you fill wine bottles with care?
snippet paragraph:
Wine filling machines are designed to handle wine gently, minimizing agitation and oxygen exposure. They often use gravity filling or vacuum filling techniques to preserve the wine's delicate flavors and aromas.
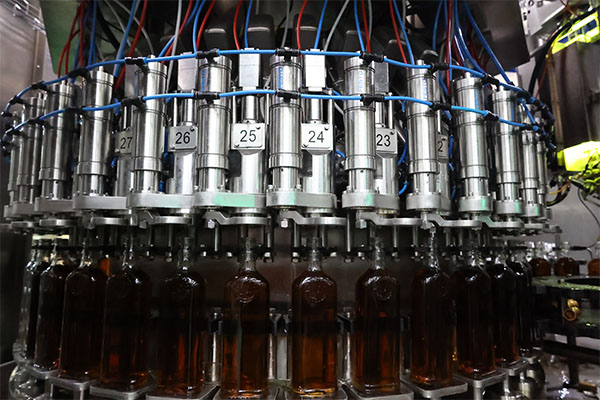
Important Aspects
- Gentle Handling: Minimizing agitation.
- Gravity or Vacuum Filling: Reducing oxygen.
- Flavor Preservation: Maintaining quality.
- Specialized Nozzles: Controlled dispensing.
- Automated Systems: Consistent performance.
- Quality Control: Ensuring fine taste.
Dive deeper Paragraph:
Wine filling machines are meticulously designed to handle wine with the utmost care, minimizing agitation and oxygen exposure to preserve its delicate flavors and aromas. The filling process is critical in wine production, as excessive agitation or oxygen contact can lead to oxidation and the development of undesirable flavors, ultimately compromising the quality of the wine. To prevent this, wine filling machines often employ gentle filling techniques such as gravity filling or vacuum filling.
Blow-Fill-Seal Combi-block Machines: Integrated Efficiency
leading paragraph:
All-in-one! How do you combine blowing, filling, and sealing?
snippet paragraph:
Blow-fill-seal combi-block machines integrate bottle blowing, filling, and sealing into a single, continuous process. This reduces handling, minimizes contamination risks, and improves overall production efficiency.
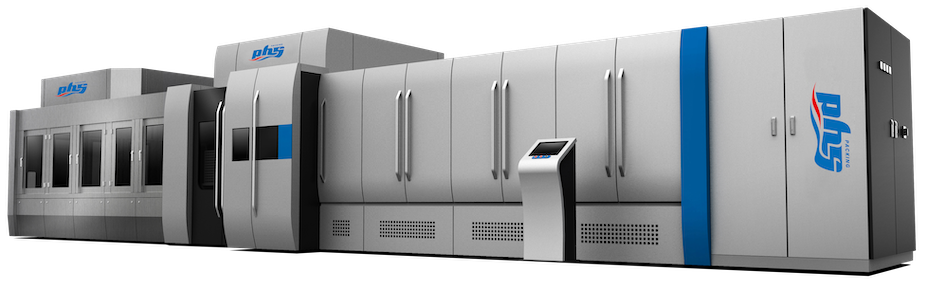
Key Advantages
- Integrated Process: Streamlined production.
- Reduced Handling: Minimizing contamination.
- Improved Efficiency: Faster output.
- Automated Systems: Consistent performance.
- Space Saving: Compact design.
- Cost Effective: Lower operational expenses.
Dive deeper Paragraph:
Blow-fill-seal (BFS) combi-block machines represent a cutting-edge approach to beverage packaging, integrating bottle blowing, filling, and sealing into a single, continuous process. This innovative design offers several advantages over traditional filling lines, primarily by reducing handling, minimizing contamination risks, and improving overall production efficiency.
Aseptic Filling Machines: Sterility Guaranteed
leading paragraph:
Germ-free zone! How do you fill beverages in a sterile environment?
snippet paragraph:
Aseptic filling machines sterilize both the product and the container separately before filling and sealing in a sterile environment. This allows for extended shelf life without refrigeration or preservatives, ideal for milk, juice, and other sensitive beverages.
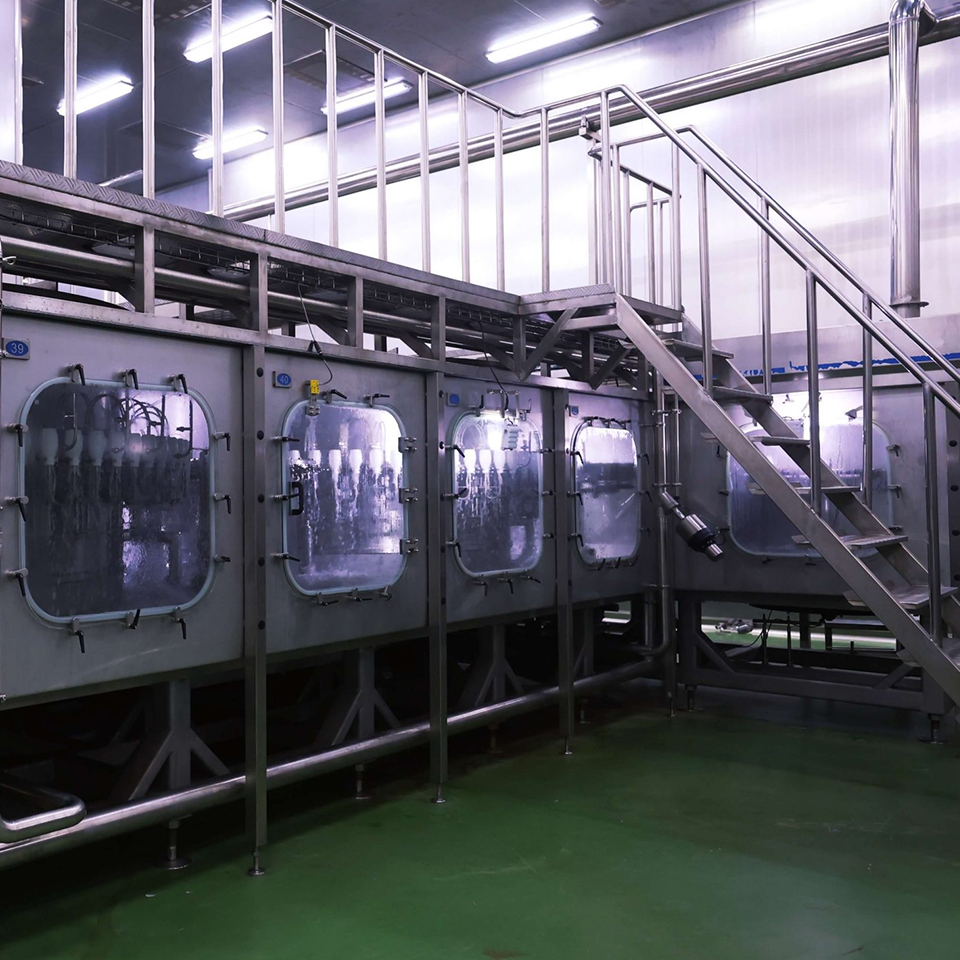
Essential for Aseptic
- Sterile Environment: Eliminating contamination.
- Separate Sterilization: Product and container.
- Extended Shelf Life: No refrigeration needed.
- Automated Systems: Precise control.
- Hygienic Design: Easy to clean.
- Quality Assurance: Safe and sterile product.
Dive deeper Paragraph:
Aseptic filling machines are designed to fill beverages in a completely sterile environment, ensuring that the product remains free from microorganisms that could cause spoilage. This technology is particularly crucial for products like milk, juice, and other sensitive beverages that are prone to bacterial growth. The key principle behind aseptic filling is to sterilize both the product and the container separately before bringing them together in a sterile zone.
Ultra-Clean Filling Machines: High-Level Hygiene
leading paragraph:
Beyond clean! What is ultra-clean filling?
snippet paragraph:
Ultra-clean filling machines provide a high level of hygiene by using advanced filtration, sterilization, and air purification techniques. They are suitable for beverages that require a longer shelf life and reduced microbial load, such as sensitive juices and dairy products.
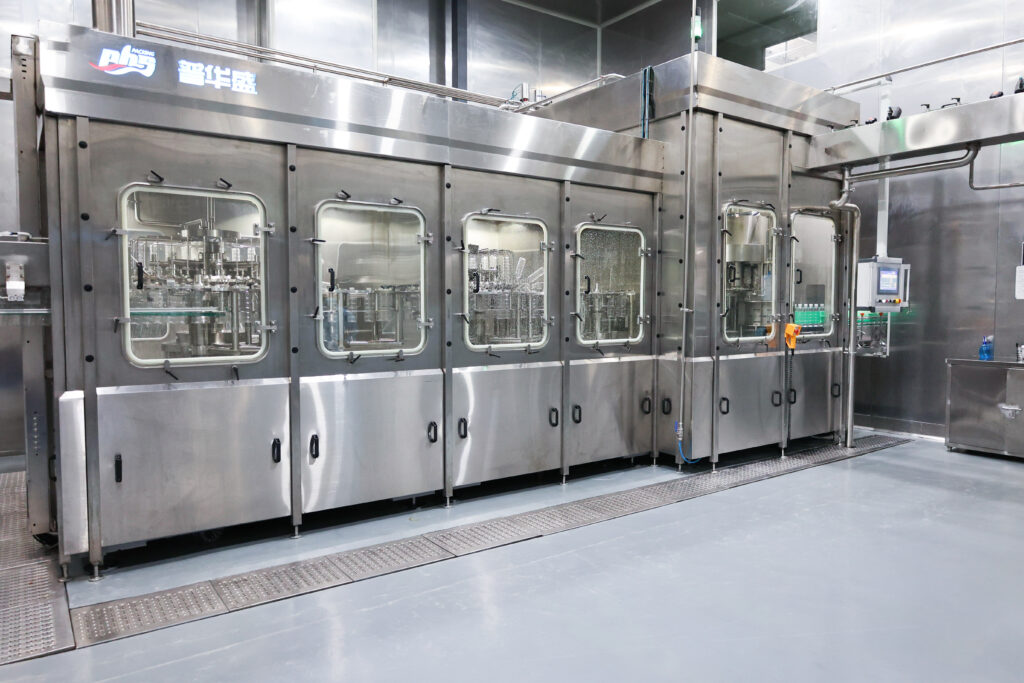
Core Features
- Advanced Filtration: Removing particles.
- Sterilization: Eliminating microorganisms.
- Air Purification: Maintaining clean air.
- Hygienic Design: Easy to sanitize.
- Automated Systems: Consistent performance.
- Quality Control: Ensuring purity.
Dive deeper Paragraph:
Ultra-clean filling machines represent the pinnacle of hygienic filling technology, providing an exceptionally high level of cleanliness through advanced filtration, sterilization, and air purification techniques. These machines are designed for beverages that require a longer shelf life and a significantly reduced microbial load, making them ideal for sensitive juices, dairy products, and other beverages that are particularly susceptible to spoilage.
Conclusion
From water to wine, the world of filling machines is vast and varied! Each type plays a vital role in getting your favorite beverages safely and efficiently to your glass.
My name is Allen, and I'm an expert in filling machine technology at EQS (eqsfilling.com), a leading liquid packaging solution provider based in China. If you're looking for top-quality filling machines for your production line, feel free to reach out to me at [email protected]. We specialize in providing customizable solutions with cutting-edge technology.