Aseptic Filling Machine
Aseptic filling technology can be applied to non-carbonated products beverage products without preservatives for long-term maintenance, high acid/low acid/neutral beverages, and PET bottle beverage products.
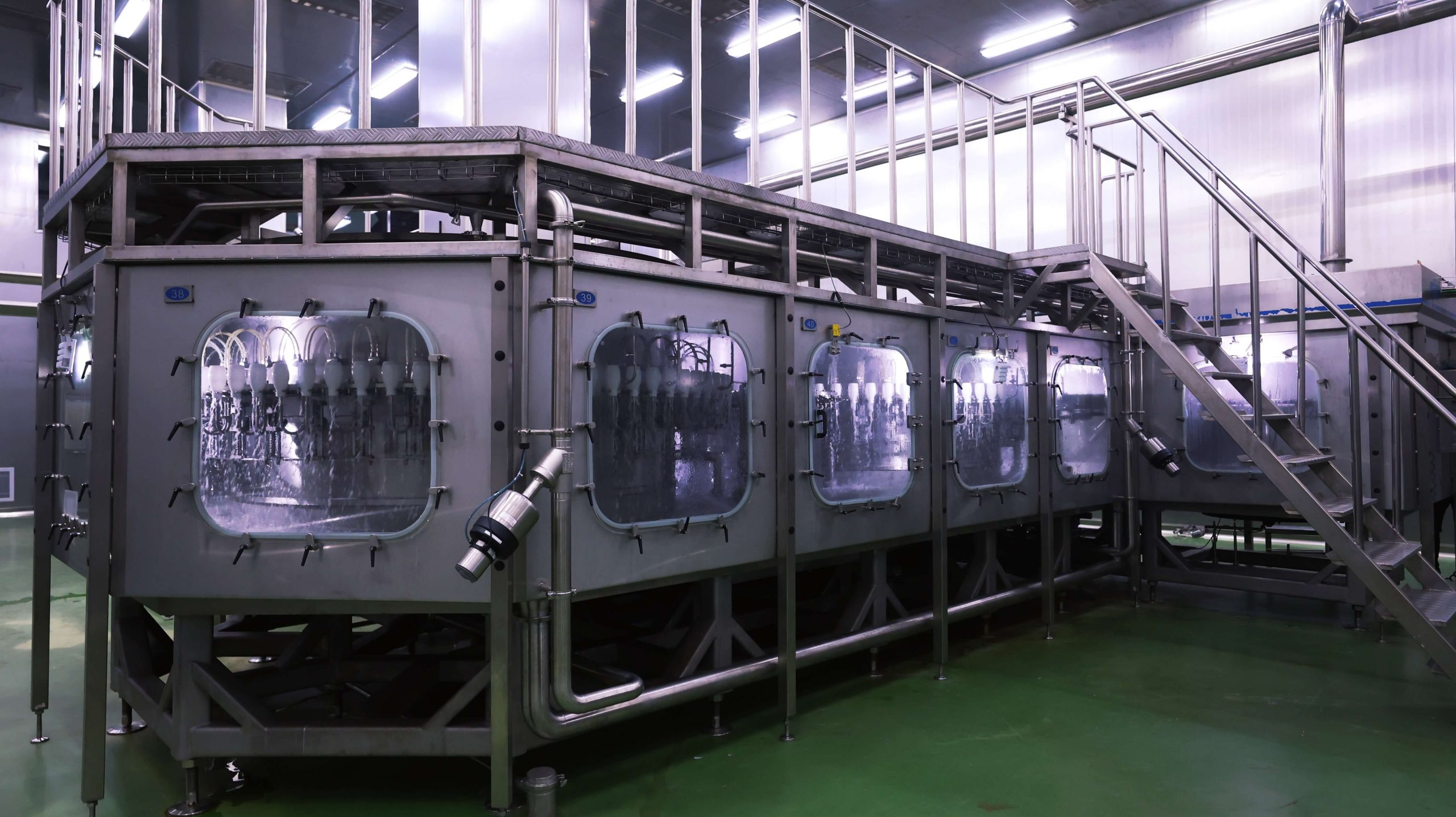
Aseptic Combiblock Introduction
Our medium-and-high-speed PET bottle aseptic cold filling technology can be applied to a wide range of beverage products. Based on the aseptic cold filling technology, the Company has developed an Aseptic Blowing-Filling-Capping Combiblock that integrates solutions of blowing bottles, packaging materials sterilization, filling and capping. The equipment has perfect package hygiene conditions and complete sterilization process. The complete isolation area guarantees the sterility in the liquid packaging process, providing the perfect packaging service for highly-and-low-acid products.
The aseptic filling line Main System
Hydrogen peroxide atomization sterilization system (For bottle sterilization)
Hydrogen peroxide water is transported to the pressurized hydrogen peroxide storage tank through the pump through the hydrogen peroxide water channel, transported by the transport pipeline to the connector of the hydrogen peroxide atomization device, the high-pressure hydrogen peroxide is sprayed into the atomization device through a special nozzle device, and then heated by the high temperature of the heating ring, the fine droplet atomized hydrogen peroxide water is rapidly heated and atomized into dry hydrogen peroxide steam, and then transported through the pipeline to the sterilization section of the capping section and the bottle atomization sterilization section.
Oil-free, water-free compressed air is sent to the compressed air inlet pipe through the pipeline, and after filtration, it is sent to the heating device, and the compressed air is heated by the heating gas and sent to the hot air decomposition section of the bottle of the capping machine.
Hydrogen peroxide atomization sterilization system for bottle cap
Hydrogen peroxide water is transported to the pressurized hydrogen peroxide storage tank through the pump through the hydrogen peroxide water channel, transported by the transport pipeline to the connector of the hydrogen peroxide atomization device, the high-pressure hydrogen peroxide is sprayed to the special heating panel of the person through the special nozzle device, and then through the high temperature heating of the heating ring, the hydrogen peroxide water is atomized, and then the atomized hydrogen peroxide water is sent to the entrance of the cap sterilization device through the heated compressed air, and the atomized hydrogen peroxide water is sprayed into the inside of the cap sterilization channel, and the cap through the cap sterilization channel is sterilized. According to the process requirements, the cap sterilization channel is divided into hydrogen peroxide atomization gas spraying section, hot air decomposition section, sterile water spray section, sterile gas spray section and cap transportation section.
Sterile material buffer storage system
It’s used to buffer and storage the sterile materials UHT treated under the sterile condition. It is used to balance the difference between the production capacity of “filling machine” and “sterilizer”.
Aseptic Combiblock System
Bottles are transferred to the filling machine through the bottle blowing machine to enter the bottle mouth and the bottle body H2O2 atomization sterilization dial to sterilize the bottle body and the bottle mouth, and then the bottle is transferred to the bottle H2O2 atomization sterilization machine. After the bottle has been spray with H2O2 for a certain time, the bottle enters the H2O2 dryer, and the atomized H2O2 in the bottle is decomposed by hot air. The hydrogen peroxide atomization sterilization machine and the hot air decomposition machine work together to achieve the purpose of disinfection and sterilization of the bottle, Then the bottles are forcibly cleaned by the sterile water bottle washing machine, and the processed empty bottles are transferred to the filling machine through the flushing and filling transition wheel. When the bottle signal detects that there is a bottle, the filling starts after passing through a certain station, and the flowmeter measures according to the set filling flow. When the set capacity is reached, the filling valve opens the slow filling procedure (different according to different machines), Until the metering volume of the flowmeter reaches the set total filling capacity, after the filling is completed, the flowmeter sends a valve closing signal, and the filling is completed. The bottles after filling are sent to the capping machine by the filling wheel.
The anti rotation knife on the capping machine blocks the bottleneck, keeps the bottle upright and prevents rotation. The capping head keeps revolution and rotation on the capping machine, realizes the actions of grasping, capping, capping and decapping under the action of the cam, and completes the whole capping process., The bottle with the cap screwed is transferred from the cap screwing machine to the bottle output conveyor chain, and then transferred from the filling machine by the conveyor chain.
The whole sterile water washing bottle, filling and capping are in the sterile isolation warehouse. The top of the filling machine is equipped with AAF efficient sterilizing filter to keep the filling and capping area always under positive pressure. At the same time, the special AAF efficient heating system is used to dry the atomization and drying sections. At the same time, the space COP/SOP system, filling and capping liquid sealing system are used together to reduce space microbial pollution
Liquid tank sealing system
The system is mainly composed of 300L water tanks, conveyor pumps, pneumatic diaphragm valves, pipelines and other parts. All parts are made of stainless steel.
This system uses pure water with a special fungicide as the tank sealing medium. The medium circulates in the sealing structure of each rotary part of the tank.It can prevent the sterilization liquid mist will occur corrosion for the bearing and other transmission parts. And it also can prevent external non clean air entering the sterile space.
The system is also equipped with COP/SOP cleaning pipeline to ensure that there is no cleaning dead zone to minimize.
CIP System
The system installs multiple sets of nozzles in the clean area of the sterilization machine, the bottle washing machine, the bottle filing machine, and bottle capping machine. The equipment surface in this area is cleaned and disinfected by injecting detergent and disinfectant online into sterile water with spraying method.When cleaning, sterile air is mixed with the detergent to achieve foam cleaning mode (COP), and the disinfection is sprayed with Peracetic acid normal temperature disinfection solution (SOP).
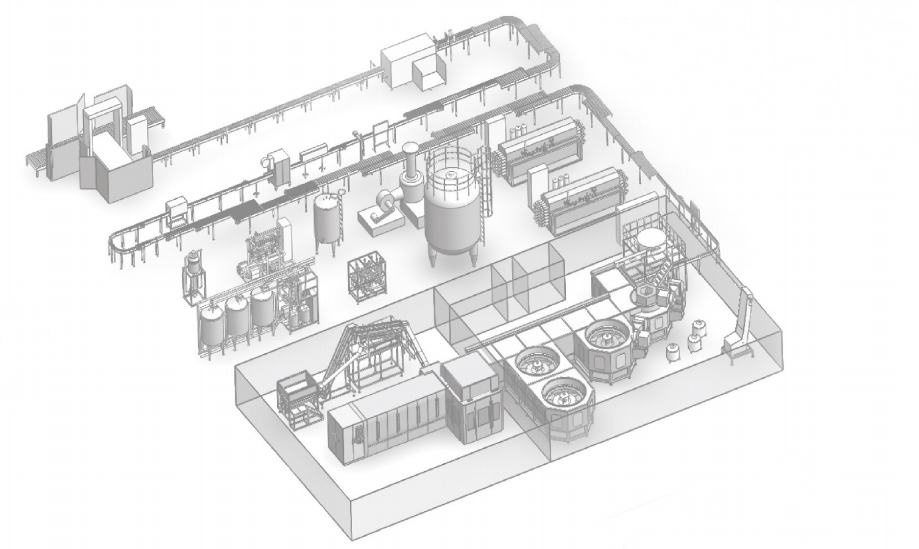
Don't hesitate to contact us for more information.
jiangsu,suzhou zhangjiagang hexi rouad - china